A major part of any plant’s operating costs are related to Maintenance Materials; in addition, if the required materials are not accessible when needed, productivity, reliability, morale and the bottom line of the plant will suffer. Spare parts management, which means “an organized maintenance storeroom”, is a key process that supports effective maintenance planning and scheduling and could improve plant reliability. Improving materials and spare parts management will increase the efficiency of the maintenance department. Various studies show that an average of 20-30% of maintenance technician time is wasted to find the needed parts and material. This course is designed to introduce the concepts of warehouse and spare parts management, so you can create a common understanding between the maintenance and the warehouse departments and this way, considering the status quo of the organization and the optimal design of the warehouse, optimize the ordering systems.
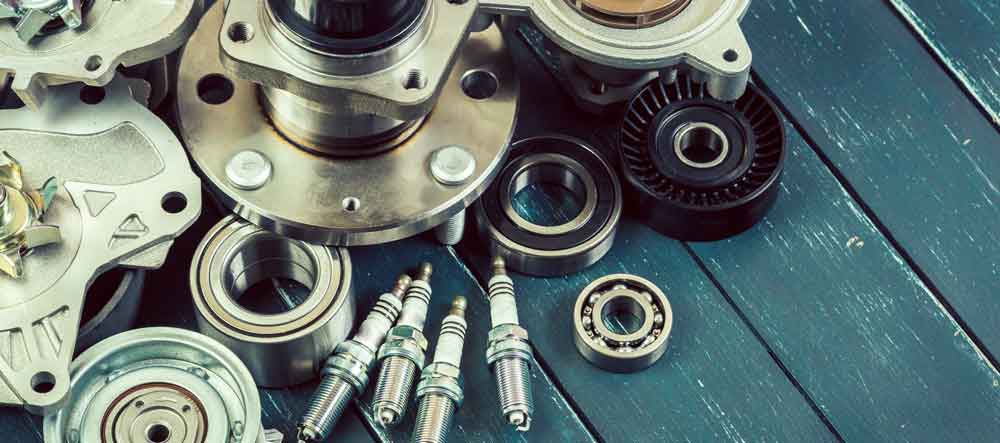
Course Overview
Target Audience
This course is designed for those in contact with inventory management and storerooms, including maintenance managers, storeroom managers, purchasing officers, storeroom personnel, supervisors, and operations and maintenance coordinators.
Learning Outcomes
By the end of this course, you will learn to:
- Identify the opportunities to increase the plant reliability and maintenance performance;
- Improve management of spare parts and materials information;
- Assess equipment criticality;
- Identify key processes in the storeroom and inventory control;
- Solve spare parts and warehouse issues;
- Arrange items in warehouses;
- Manage low-consumption and high-consumption parts;
- Optimize the order point and order quantity for high-consumption items;
- Optimize the inventory of low-consumption items;
- Assess the related risks;
- Determine surplus items; and
- Monitor warehouse KPIs.